Digital twin technology has been used for years by the manufacturing and aviation industries to predict potential problems and avoid them before they result in an unsafe product. Now, the construction industry is beginning to use digital twins for similar purposes. By doing so, construction companies can improve safety, efficiency, and profitability not only on the job site, but also in other areas of their business.
Digital Twins have already gained considerable traction in construction since last year following the availability and adoption of BIM (Building Information Modeling), AI, drones, and the Internet of Things (IoT).
With the advent of new technology, contracting firms began to capitalize on it and have adopted Digital Twins among their top firms. This has become widely accepted by top contracting firms.
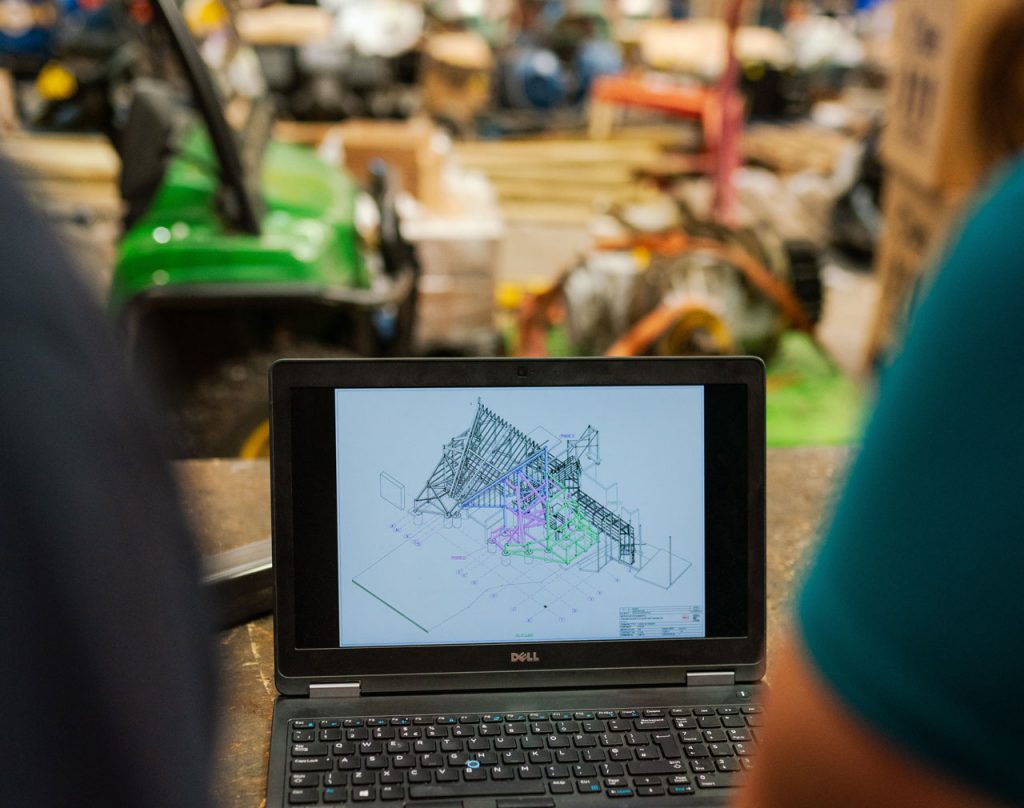
Using digital twins, worksite management becomes easier since they help track all the moving parts and resources, alerting you to possible issues with material and labor allocation. Managers can easily control and assess budgetary balancing at their locations.
Management can use this information to keep projects on track, ensure that they remain within the budget and ensure smooth operations.
Digital Twins provide a number of benefits to managers in terms of improving communication between those on the project site and those at the contracting company.
During construction, having a live feed of all components at hand, from IoT-enabled machines to inventory and location of materials, as well as a constantly-updating live model of the structure itself, is an extremely useful tool.
In addition to monitoring the construction phase, the software also keeps tabs on its cost and profitability throughout its lifetime.
A Digital Twin of the building is a product of high value that will be delivered after construction. A virtual structure with its built-in AI can be passed to the client for their own use throughout the structure's lifespan.
Owners can access their buildings' data using it, and make informed decisions on future improvements and optimum building utilization based on the insights they gain.
Once a client gains control, the Digital Twin monitors its fully built counterpart and alerts building managers for potential emergencies, especially in high-risk settings like airports and hospitals.
Through its ability to detect potential problems in connected systems such as HVAC (Heating, Ventilation, and Air Conditioning) and electrical, Twins help prevent disasters from happening.
However, they're not just good for disaster aversion. There are a lot of applications that twins can be used for since they collect data all the time. A retail structure may monitor foot traffic, sales, and room temperatures and communicate that information to optimize conditions that encourage sales.
In a large facility with multiple departments, measuring the use of space can be useful for optimizing the allocation of space for cramped departments and less populated areas so each department is able to perform at maximum capacity.
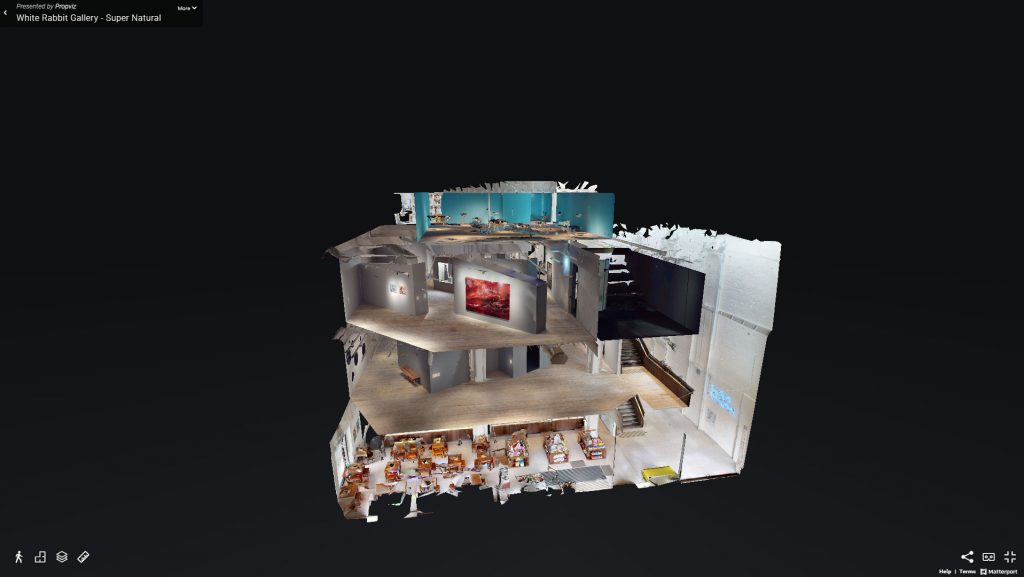
In the field of BIM and Digital Twins, 42 Interactive is implementing leading technologies because we understand the considerable advantages BIM and Digital Twins can provide us, as well as our clients.
Delivering the best end product possible is our priority. If you'd like to learn more about how a Digital Twin can help you maximize the usability of your current structures or get started on a new design plan, we're always delighted to assist.